Nur mit objektiven Daten kann die Arbeit laufend optimiert werden
Dariusz Koczara hat TMS-Lösungen in mehreren Unternehmen aus verschiedenen Branchen implementiert. Für ihn ist die Erfassung spezifischer, objektiver Daten über die tatsächlichen Betriebsparameter von Maschinen entscheidend für den Prozess der Betriebsoptimierung.
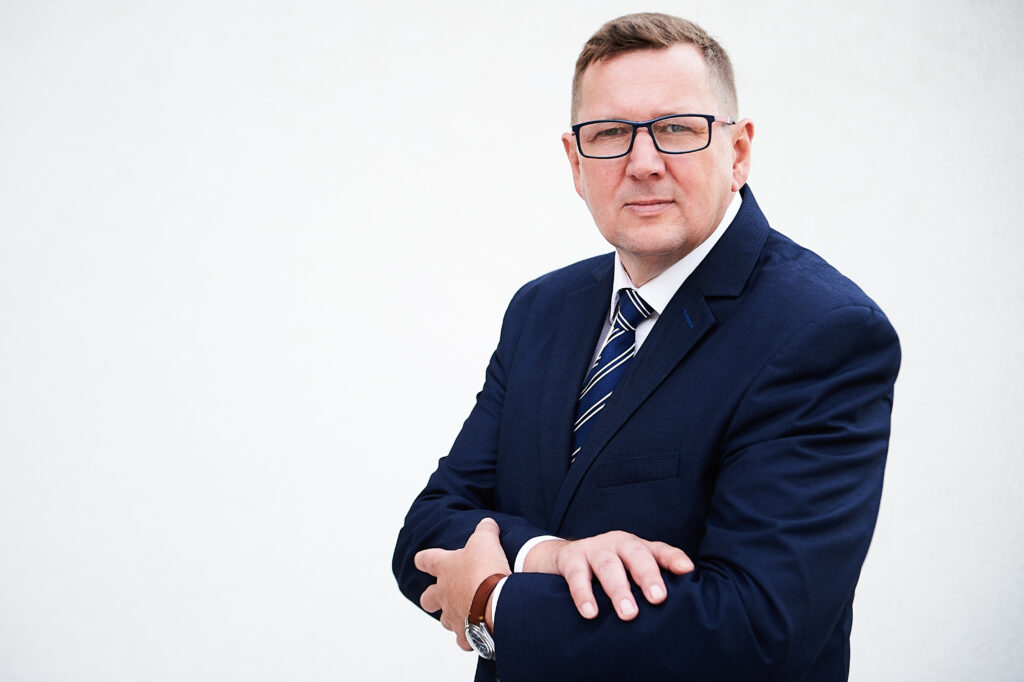
Sie haben die TMS-Plattform in mehreren Unternehmen eingeführt. Wo hat es angefangen?
Im Jahr 2007 begann ich als leitender Maschinenbauingenieur mit einer Analyse des Betriebs von Maschinen in 16 Tagebauen. Aus meiner früheren Berufserfahrung war mir klar, dass nur objektive Informationen über den Betrieb der Maschinen eine ordnungsgemäße Wartung und Zuverlässigkeit ermöglichen. Ich wollte konkrete Daten erhalten, um den Betrieb auf zuverlässige Weise verbessern zu können. Ich war auf der Suche nach einer Lösung, die solche Informationen an einem Ort bereitstellen würde. So bin ich auf TMS gestoßen.
Damals steckte die Bereitstellung von Informationen aus Telemetriesystemen für mobile Maschinen im Bergbau noch „in den Kinderschuhen“. Was hat Sie dazu bewogen, diese Zusammenarbeit fortzusetzen?
Das TMS verfügte bereits über Lösungen zur Übertragung von Daten über GPS/GSM von der Maschine direkt zu den Servern. Ein weiterer Aspekt war, dass das System an Maschinen verschiedener Typen und Hersteller angeschlossen werden konnte. Damals beschloss ich, die TMS-Plattform auf fast 100 Maschinen zu implementieren. Die erste Berechnung ergab, dass sich die Investition nach etwa 12 Monaten amortisieren würde, die endgültige Amortisation lag bei weniger als 11 Monaten. Während der Umsetzung haben wir eine Reihe von Analysen des Maschinenbetriebs und der Arbeitsweise der Bediener durchgeführt. Es stellte sich heraus, dass die Unterschiede beim Kraftstoffverbrauch bei denselben Arbeitsgängen bis zu 30 % betrugen. Mit diesen objektiven Daten begannen wir, die Bediener zu schulen und mit ihnen zu sprechen.
.Hat sich die Plattform Ihren Bedürfnissen entsprechend entwickelt?
Unser internes Problem war die Überwachung und Analyse von Daten. Deshalb wollten wir das System flexibler gestalten. Das TMS lieferte uns automatisch erstellte, spezielle Berichte. Jeden Tag erhielten wir Informationen darüber, wie die Arbeit des vorangegangenen Tages gelaufen war. Wir konnten sehen, was passierte, und die Bediener konnten ihr Verhalten an der Maschine korrigieren. Wir konnten den gesamten Prozess, der mit dem Betrieb einer bestimmten Maschine verbunden ist, analysieren. Die Kombination aus dem Managementansatz und der Lieferung fertiger Analysen, ohne dass wir die Plattform aufsuchen mussten, führte zu wesentlich größeren Einsparungen.
Das bedeutet, dass Sie über das typische Muster eines Kundendienstleisters hinausgegangen sind.
Auf jeden Fall. Wir trafen uns vierteljährlich mit TMS und legten dar, was für uns funktioniert, womit wir Probleme haben, was wir ändern und umsetzen wollen. Wir analysierten die Möglichkeiten, welchen Weg wir einschlagen sollten und ob es Möglichkeiten gab, die Plattform an unsere Bedürfnisse anzupassen. Es war ein gemeinsames Bemühen, neue Lösungen zu entwickeln.
Am Anfang ging es nur darum, die Effizienz mobiler Maschinen zu steigern. Am Ende wurden jedoch viel mehr Vorteile erzielt?
In der ersten Phase unserer Zusammenarbeit erzielten wir Kraftstoffeinsparungen und optimierte Prozesse. Da wir jedoch wussten, dass das TMS in der Lage war, unsere Ideen anzupassen und umzusetzen, begannen wir, die Plattform für das Management zu nutzen – wir extrahierten Informationen und nutzten sie zur weiteren Verwendung in unseren Prozessen. Wir verknüpften unser KPI-Überwachungssystem, und von da an erhielten wir für alle Maschinen spezifische Informationen über sie. Wir sind von einem relativ einfachen Programm dazu übergegangen, KPIs zu analysieren, Berichte zu erstellen und die Ursachen von Maschinenausfällen und Problemen zu ermitteln.
War der nächste Schritt die Implementierung des TMS MES, d.h. die Anbindung der Plattform an die Verarbeitungsbetriebe?
Ja, bei der Analyse stellte sich heraus, dass wir keine optimalen Informationen darüber hatten, wie unsere Verarbeitungsanlagen arbeiten. Wir begannen, Informationen von Waagen, Schalttafeln und Produktionssystemen zu sammeln. Im Jahr 2012 begannen wir mit einer großen Investition, um eine ganz neue Anlage zu bauen. Dort installierten wir eine TMS-Plattform, die es uns ermöglichte, objektives Wissen über den Betrieb der Anlage zu erhalten. Wir konnten Prozesse verfolgen und hatten konkrete Daten. Das war schon ein anderes Niveau – wir achteten auf die Leistung, wie der Betreiber die Anlage steuerte und wie sie sich auf den Betrieb übertrug. Mit objektiven und zuverlässigen Daten konnten wir den Betrieb der Anlage kontinuierlich optimieren.
Mit kleinen Schritten haben Sie die Bergwerke in die digitale Realität gebrachtital age.
Der springende Punkt ist, dass wir 16 Bergwerke in ganz Polen hatten. Wir wollten genau wissen, wie diese Niederlassungen funktionieren, und sie auf der Ebene der Zentrale analysieren. Während des gesamten Prozesses war es das Wichtigste, objektive Informationen über die tatsächlichen Parameter zu erhalten.
So konnten wir die nächsten Schritte unternehmen – eine weitere Anlage wurde erstellt und an die TMS-MES-Plattform angeschlossen. Unter Berücksichtigung aller Erfahrungen implementierten wir dann TMS MES auf allen Produktionslinien in Polen und automatisierten die KPI-Berichterstattung auf der Grundlage der Unternehmensstandards. Dies hob die Bergwerke auf eine völlig neue Ebene. Ich freue mich auch sehr, dass unsere Erfahrung und Beratung von der rumänischen Niederlassung genutzt wurde, wo in Zusammenarbeit mit uns ebenfalls TMS-Lösungen in allen Bergwerken des Landes eingeführt wurden.
Hier endet Ihr berufliches Abenteuer im Tagebau, aber in Ihrem nächsten Job, der mit der Recyclingindustrie zu tun hat, haben Sie ebenfalls die TMS-Plattform eingeführt?
Auf der Grundlage meiner Erfahrung und der Kenntnis der Möglichkeiten von TMS begannen wir mit der Implementierung der Plattform an 10 Standorten in der Recyclingbranche.
Das Konzept basierte wiederum darauf, objektive Informationen über den Betrieb von Geräten wie Kränen und Pressenscheren zu erhalten, von denen einige mit Diesel und andere mit Strom betrieben wurden. Auf diese Weise konnten wir die KPIs überwachen und nach weiteren Einsparungen suchen. Wir erhielten wichtige Informationen: wann die Maschine startete, wie viel sie arbeitete und Kraftstoff oder Strom verbrauchte. Auf dieser Grundlage begannen wir, Optimierungsmaßnahmen zu ergreifen. Die nächste Stufe der Verbesserungen bestand in der Implementierung einer Lösung zur Analyse der einzelnen Pressenzyklen. Dabei haben wir nicht nur die Messung ergänzt, sondern vor allem zusätzliche Analysewerkzeuge entwickelt – eine grafische Visualisierung des Verlaufs der Zyklen für das Zerkleinern, Verdichten und Schneiden von Schrott sowie eine zusätzliche Reihe von KPIs.
Als Sie mit der Implementierung an einem neuen Standort begannen, haben Sie die Plattform erneut an die neuen Anforderungen angepasst?
Ja, das TMS verfügte nicht über diese Funktion, und wir suchten erneut nach einer Möglichkeit, die Kontrolle des gesamten Prozesses zu automatisieren.
Da wir auch Informationen darüber erhalten wollten, wie viel uns der Transport von Kunden tatsächlich kostet, und um die Rentabilität des Preisniveaus für die Lieferung einer Tonne Schrott zu ermitteln, begannen wir mit der Überwachung der Lastwagen, die Schrott transportieren. Das System selbst lieferte uns Informationen darüber, wohin der Lkw fuhr, zu welchem Kunden er fuhr, wie viele Kilometer er zurückgelegt und wie viel Kraftstoff er verbraucht hatte und wie lange es dauerte, den Schrott mit dem HDS am Abholort zu laden, und generierte schließlich die von uns gewünschten Informationen.
Wie hilft die Plattform im Arbeitsalltag?
Betrachtet man das gesamte Prisma der Arbeit mit einem TMS, so ist die Automatisierung und der Übergang zu Industrie 4.0 und 5.0 der Schlüssel. Eine große Hilfe ist, dass das System die Informationen selbst generiert, ohne dass ein Mensch in jeden Schritt der Berichtserstellung involviert ist. Darüber hinaus ist die Zuständigkeit für einzelne Maschinen zu jedem Zeitpunkt gegeben – automatische Versendung von Textnachrichten und Benachrichtigungen an Manager oder Vorarbeiter, wenn etwas an einer Maschine passiert, was eine sofortige Reaktion ermöglicht.
Wie beurteilen Sie Ihre bereits 18-jährige Zusammenarbeit mit dem TMS-Team?
Sehr gut, es ist ein professionelles Unternehmen, offen für Veränderungen und Zusammenarbeit. Jetzt, in meiner neuen Position als Leiter der Abteilung Energie und Maschinenbau in einem Unternehmen, das für KGHM arbeitet, blicke ich bereits in die Zukunft und beginne darüber nachzudenken, wie wir TMS in unseren Betrieben einsetzen können. Und an Herausforderungen mangelt es nicht – Arbeiten unter Tage, ohne Internet, Geolokalisierung und GSM. Wir fangen an, in einem anderen Unternehmen zusammenzuarbeiten, und wir werden bestimmt eine Lösung finden.
InterviewerIn Sabina Szewczyk-Wajda
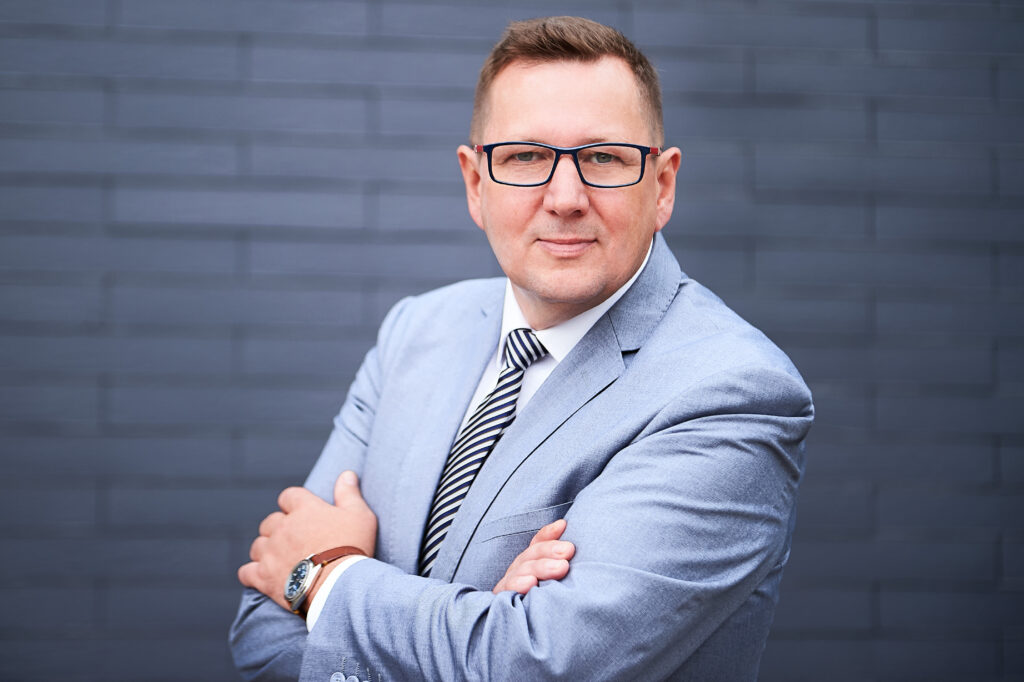
Dariusz Koczara: Als Experte für Automatisierung und Organisation von Produktionsprozessen hat er seine beruflichen Fähigkeiten in Unternehmen wie KGHM Polska Miedź S.A., Lafarge Holcim Polska S.A. und Centrozłom Wrocław S. A. eingesetzt. Er arbeitet seit 18 Jahren bei TMS.
.