The introduction of the TMS Platform at Tomaszowskie Kopalnie Surowców Mineralnych, part of the Quarzwerke Group, has enabled the company to operate in a balanced way – effectively integrating quantity, quality, and cost management. According to Andrzej Grodzki, Plant Manager at TKSM Biała Góra – one of the largest quartz sand mines in Europe – the key benefit is the increased transparency of operations made possible by the platform.
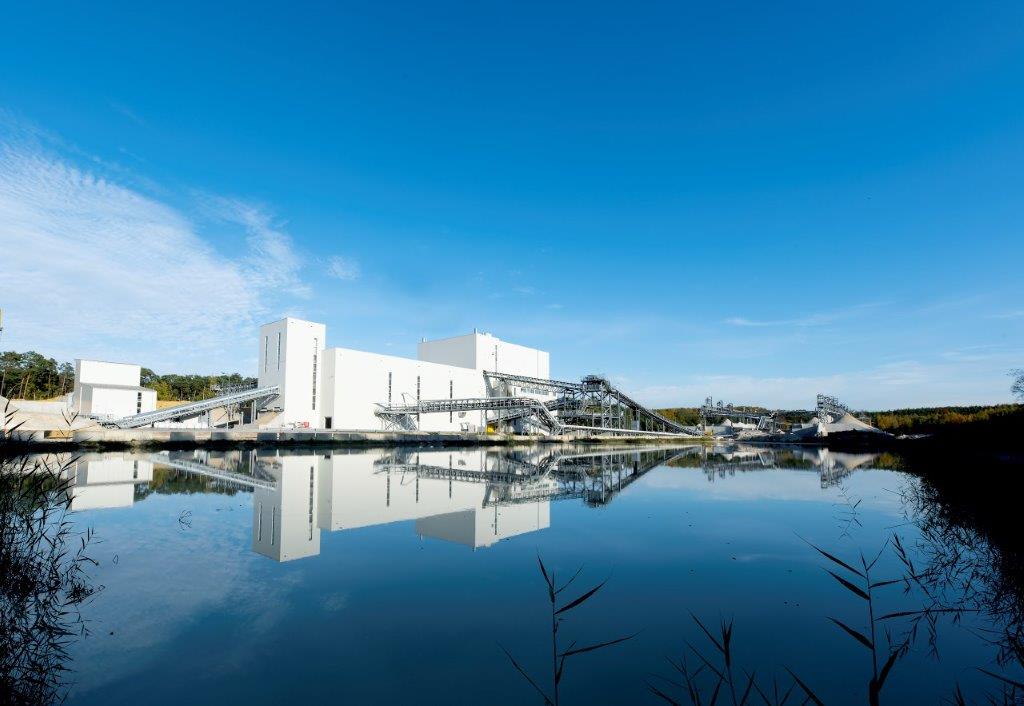
How did your relationship with TMS begin?
When I joined the company nearly 11 years ago, TMS solutions were already in place. Initially, our collaboration focused on monitoring the fuel consumption of mobile machines, as there were challenges with proper accounting. This issue became the first area of focus.
For a long time, this remained the sole purpose of the system, but our cooperation has evolved significantly since then. Today, the TMS Platform supports many more operational areas. It was first implemented 13 years ago and continues to operate effectively to this day.
To what extent have you implemented the TMS Platform at Biała Góra?
We communicated our specific needs, and TMS responded by developing entirely new functionalities within the platform – custom-made solutions that are now part of the company’s standard offering. One of the key implementations was the automated billing of transport services carried out by tippers. This includes tracking loading and unloading locations, as well as automatically calculating payments due to subcontractors.
Previously, we faced considerable challenges with this process. The transport of sand from the mine to the processing plant is handled by an external company, and billing rates vary depending on the distance. Since we operate several mines with differing transport distances, accurate tracking was essential.
We required an automated system that could provide reliable data on the actual performance of the machines – showing which pit a truck departed from, its destination, the number of trips made between those points, the total cargo transported, the applicable rates, and the key performance indicators (KPIs) for each transport operation.
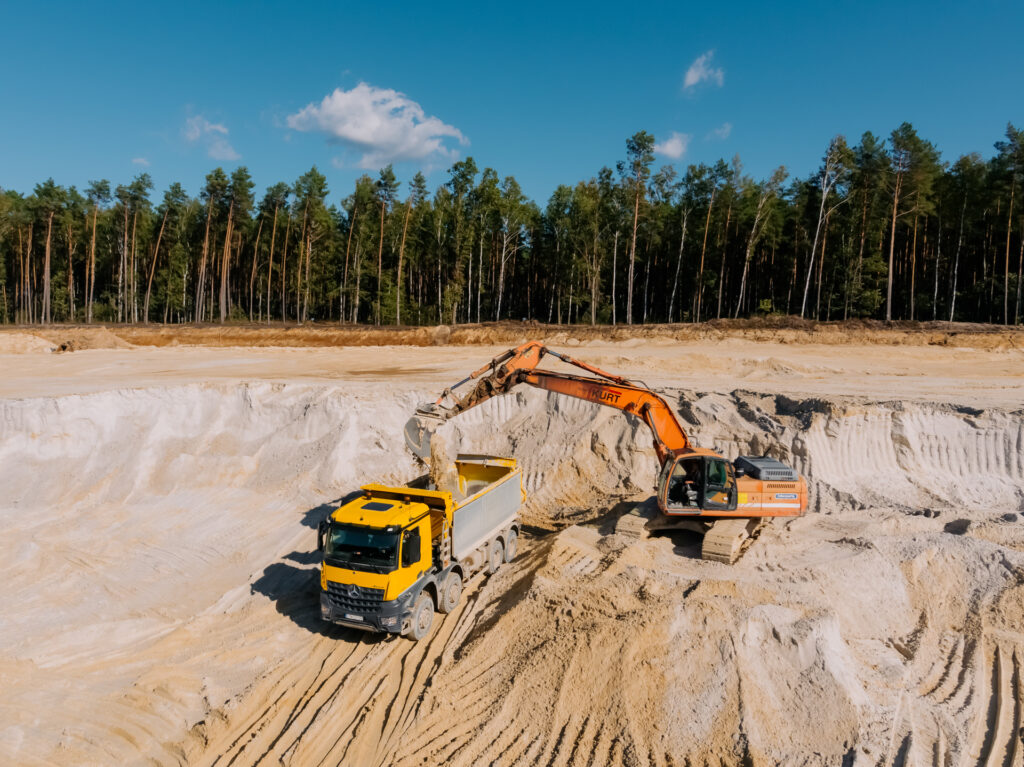
Has the newly built Biała Góra plant been equipped with modern metering solutions?
Yes. In 2021, we launched a completely new processing plant – built entirely from the ground up. It was a major investment and has been equipped with an extensive array of sensors. Our goal was to capture as much data as possible in order to analyse key production parameters, such as capacity, scale measurements, and electricity and gas consumption.
These are critical factors that directly impact our operational costs. While the raw data is collected through our internal systems, it is the TMS Platform that transforms it into KPI visualisations and tailored reports, supporting effective decision-making..
You started with a fairly simple study of fuel consumption and are now finally monitoring production and productivity. What other benefits are you observing?
Initially, the focus was solely on controlling fuel consumption. Since then, the fuel consumption per machine has decreased, and we are now successfully avoiding stock shortages – resulting in real cost savings.
By implementing this solution, we have gained transparency and reliability in tracking fuel usage, along with full real-time control over the rate at which fuel is consumed.
What about the other implementations?
Our subsequent implementations have focused on increasing transparency and reducing our daily workload. Thanks to the platform, we no longer need a large team to handle calculations, as the system provides ready-made, easy-to-understand reports.
It also supports us in discussions with subcontractors – real-time data collection allows us to quickly verify and resolve any transport issues. Additionally, we can effortlessly monitor plant performance and efficiency. With reliable data and continuous monitoring of key parameters, we can effectively keep production costs under control.
Moreover, it’s not only production that benefits. The system simplifies monthly account management, eliminating the need for manual meter readings and data analysis. At the end of each month, we receive a single comprehensive report that we pass on to the controlling department.
In summary, the main benefits are reduced workload, faster billing, improved cooperation with external companies, and – most importantly – unprecedented transparency in operations.
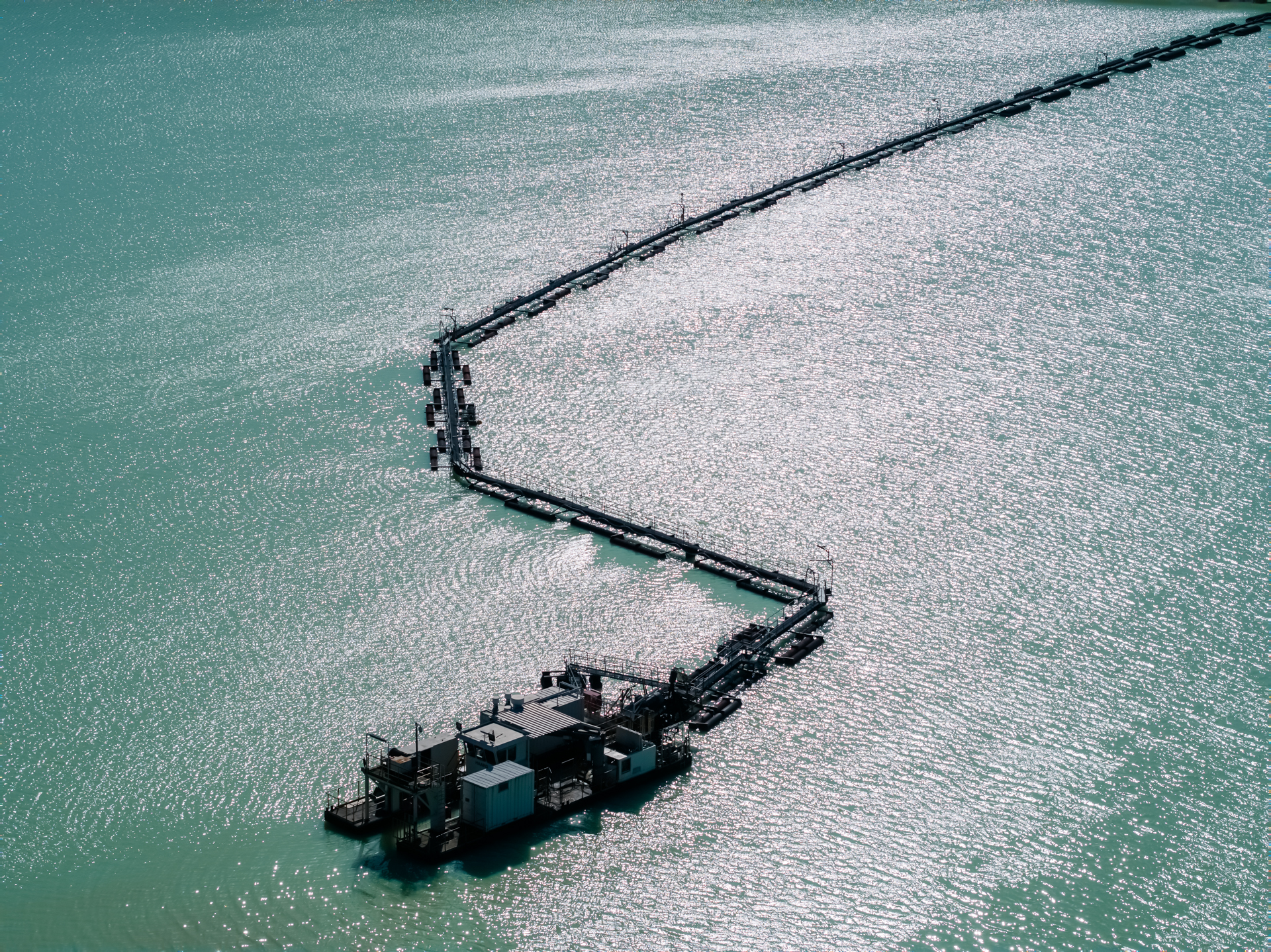
Does the fact that data is transferred Just In Time have an effect?
By monitoring ratios and tracking targets in real time, we can quickly identify areas that require attention and take corrective action. Without such a system, reacting would be much more difficult or significantly delayed. Because data is delivered almost instantly, we have a real-time overview of all key indicators.
We use daily, weekly, and monthly reports, which provide a comprehensive analysis and ultimately lead to cost savings. Production staff and shift managers have full visibility of all metrics, enabling us to run the company in a balanced way – effectively combining three crucial aspects: quantity, quality, and costs.
Can you give any specific example of using the TMS Platform?
As an energy-intensive plant, every cubic meter or kilowatt-hour counts. For example, if we use too much gas per tonne of dried sand, we receive immediate feedback from production identifying the cause. It could be equipment malfunction, allowing the maintenance team to respond quickly, or it might be due to feeding sand with too high moisture content into the drying process. After addressing the issue, we can adjust the material parameters accordingly.
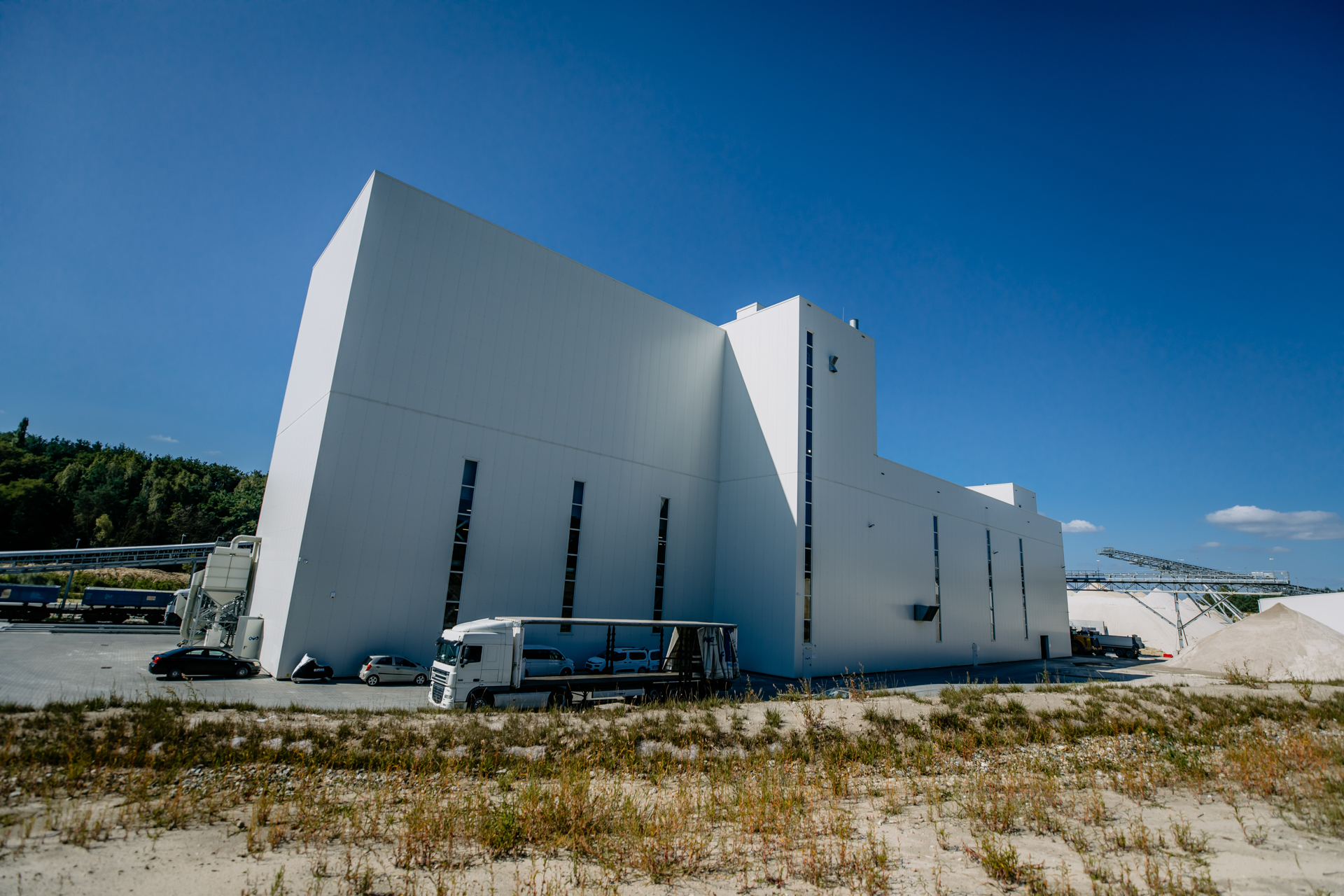
What is it like working with the TMS team?
TMS is a reliable partner who understands our needs and quality expectations – and consistently meets them. Our relationship has developed over many years, with direct and collaborative communication. The company is flexible and strives to accommodate our requirements, creating a strong sense of stability through close cooperation.
Interviewed by Sabina Szewczyk-Wajda
Andrzej Grodzki, Site Director at Tomaszowskie Kopalnie Surowców Mineralnych Biała Góra.
A graduate in Mechanical Engineering from Wrocław University of Technology, he has nearly 11 years of experience in the open-cast mining industry. Previously, he managed industrial plants in the machinery manufacturing sector, among others.